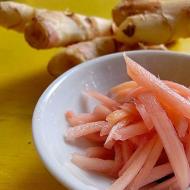
Методы дефектоскопии. Ведомость дефектов
Дефектоскоп – это электронное устройство, предназначенное для обнаружения скрытых дефектов в твердых изделиях. Прибор позволяет диагностировать отклонения от нормы без создания нагрузки или разрушения изучаемого объекта. С его помощью можно оценить однородность структуры изделия, наличие на его поверхности послаблений в результате коррозии, отклонения химического состава или наличие микротрещин.
Где используется дефектоскоп
Дефектоскопы используются в машиностроении и строительстве. С их помощью проверяются различные узлы и агрегаты, а также заготовки. Эти приборы являются незаменимыми в нефтегазовой промышленности и энергетике. С их помощью проверяются трубы и цистерны на наличие слабых стенок. Данное оборудование позволяет выявлять брак, что исключает его применение на строительстве ответственных объектов. С помощью дефектоскопов можно контролировать надежность сварных швов, слоя клея или плотность пайки.
Это оборудование производится в переносном и стационарном варианте. Отдельные модели позволяют ввести сканирование даже тех объектов, которые двигаются на высокой скорости. Такие приборы применяются для проверки труб, которые протягиваются через область сканирования. Также существуют большие дефектоскопы, передвигаемые на вагонетке по рельсам. Эти приборы используются в строительстве и промышленном производстве, в частности самолетов и кораблей. Существует масса видов дефектоскопов адаптированных под определенные условия эксплуатации. В металоперерабатывающей промышленности применяются устройства, которые могут выявлять дефекты в разогретых металлических заготовках.
Конструкции дефектоскопов
Для обеспечения работы дефектоскопа используются различные физические явления, природа которых существенно отличаются друг от друга. В связи с этим существует масса конструктивных особенностей этих приборов.
Среди самых распространенных дефектоскопов, которые массово производятся, можно выделить:
- Акустические.
- Магнитопорошковые.
- Вихретоковые.
- Феррозондовые.
- Электроискровые.
- Термоэлектрические.
- Радиационные.
- Инфракрасные.
- Радиоволновые.
- Электронно-оптические.
- Капиллярные.
Каждый из этих типов оборудования обладает своими сильными сторонами и слабостями. В связи с этим они могут подходить идеально для одних целей, но быть непригодными для других. Чтобы сделать правильный выбор дефектоскопа, важно предварительно разобраться с принципом действия каждой разновидности.
Акустический дефектоскоп
Также называется импульсным или ультразвуковым. Он работает по принципу эха. На изделие, которое тестируется, направляется короткий ультразвуковой импульс, после чего его колебания регистрируются. В результате на экран выводится карта дефектов. Этот прибор является одним из самых востребованных. Он дает вполне четкую картину тех дефектов, которые скрыты на поверхности. К достоинствам подобного оборудования можно отнести то, что оно работает с разными материалами. Существует масса подвидов акустических дефектоскопов, которые также работают от ультразвуковой волны.
Магнитопорошковый дефектоскоп
Применяется для контроля деталей различных форм. С его помощью можно сканировать сварные швы и углубления, получаемые при сверлении. Важный недостаток метода заключается в том, что он позволяет проверять только поверхностные отклонения. Он не сможет определить внутренние проблемы, если они не имеют внешнего выхода. Для обеспечения сканирования деталей применяется специальный порошок, который рассредоточивается по поверхности объекта и заполняет имеющиеся в нем неровности и трещины. После этого проводится сканирование магнитного поля, что позволяет находить место наибольшего скопления порошка. Это позволяет создавать карту дефектов, поскольку порошок не задерживается на нормальных гладких поверхностях, а забивается в неровности
Недостаток данного метода заключается в том, что для него необходимо покупать магнитный порошок. Он является расходным материалом, поэтому быстро заканчивается и высыпает в роли грязи, которую нужно периодически собирать.
Вихретоковые дефектоскопы
Действуют по физическому принципу вихревых токов. Данный аппарат возбуждает вихревые токи в зоне тестирования, после чего анализирует состояние объекта по их поведению. Данный метод является одним из самых неточных. Глубина контроля трещины составляет до 2 мм. В связи с этим получить объективную картину действительного состояние измеряемой поверхности сложно.
Феррозондовый дефектоскоп
Вырабатывает импульсы тока, которые посылаются на изучаемую поверхность. По их поведению происходит анализ имеющихся дефектов. Данное оборудование является довольно чувствительным и может выявлять неровности с глубиной от 0,1 мм. Данным оборудованием осуществляется контроль качества литых деталей, металлопроката и сварочных соединений.
Электроискровые дефектоскопы
Создают электрический разряд между своим чувствительным щупом и изучаемой поверхностью. Щуп представляет собой пучок электродов, что увеличивает площадь изучения. Разряды пробиваются через воздушный промежуток между поверхностями. В результате осуществляется создание карты изучаемого объекта с отмеченными повреждениями. Для обследования таким методом необходимо чтобы объект изучения был изготовлен из токопроводящего материала.
Термоэлектрический дефектоскоп
Работает по физическому принципу электродвижущей силы, которая возникает при нагреве участка контакта между двумя различными материалами. Данное оборудование является одним из самых дорогостоящих, поскольку требует использование высококачественных материалов, которые позволяют фиксировать минимальные изменения температуры между эталоном и изучаемой поверхностью.
Радиационные
Осуществляют облучение объектов рентгеновскими лучами и нейтронами. Они работают по такому же принципу что и применяемый в медицине рентген аппарат. В результате получается радиографический снимок или светлое изображение на экране прибора. Данное оборудование является небезопасным для оператора, поскольку рентгеновские лучи неблагоприятно влияют на здоровье. Прибор позволяет проводить действительно глубокое изучение объектов, но может применяться далеко не на всех материалах.
Инфракрасные
Отправляют тепловые лучи, которые отбиваются от поверхности объекта и позволяют анализировать отклонение от нормы. На экране прибора просматривается тепловая карта, где участки с дефектами имеют измененные цвета. Данное оборудование позволяет выявлять дефекты, но не дает точной картины об их характеристиках. Тяжело определиться с глубиной трещин, поскольку рассматриваются только очертания нарушенных участков.
Радиоволновые
Генерируют радиоволны, которые направляются на предмет изучения. Потому как они отбиваются от предмета, можно определить не только трещины или утолщение, но и диаметр и даже толщину изоляционного покрытия. Подобное оборудование применяется для работы с металлами и другими материалами.
Электронно-оптические
Применяются для контроля объектов, которые находятся под высоким напряжением. Ими пользуются электромонтажники. Подобное оборудование позволяет не только выявить места перелома проводов, но и качество работы изоляции.
Капиллярное дефектоскопирование
Подразумевают покрытие изучаемой поверхности специальным индикаторным веществом, которое заполняет имеющиеся микротрещины. В тех местах, где толщина вещества больше, его цвет более насыщенный в сравнении с ровными участками. По этим цветам визуально определяются углубления. Этот метод подразумевает использование не электронного прибора, а только индикаторное вещество и лупу или микроскоп.
Критерии выбора
Выбирая дефектоскоп, следует обратить внимание на некоторые характеристики, которые являются ключевыми. В первую очередь нужно ориентироваться по диапазону измерения. Разные модели отличается чувствительностью. Самое точное устройство способно выявлять дефект, глубина которого составляет всего 1 мкм. Для определенных целей такая чувствительность действительно нужна, но для прочих является излишней. К примеру, если необходимо найти микротрещины на коленвале или других вращающихся деталях, то лучше использовать точное оборудование. Если же нужно проанализировать состояние металлического каркаса в строительстве, то подобные микротрещины не столь важны. Учитывая толщину тела арматуры или балок, маленький дефект глубиной 1 мкм никак не сможет стать причиной того, что металл лопнет, особенно если он используется в тех целях, для которых предназначен.
Также выбирая дефектоскоп, следует ориентироваться по тому, для каких материалов оно предназначено. Одни модели могут работать только с металлами, в то время как другие являются универсальными. Также по отношению к дефектоскопам важным понятием является производительность. Она показывает скорость сканирования. Чем она выше, тем быстрее можно оценить состояние объекта. Если ориентироваться по данному показателю, то безусловными лидерами являются вихретоковое и феррозондовое оборудование. Если использовать магнитопорошковый прибор, то продолжительность диагностики займет много времени, к тому же возникнет необходимость растирать порошок.
Рассматривая дефектоскопы, стоит в первую очередь отдать предпочтения ультразвуковым приборам. Они не несут вреда для оператора как радиационные, при этом дают вполне достаточное представление об имеющихся дефектах и целесообразности отправки детали в выбраковку.
Лекция N 10
Дефектоскопия – это область знаний, охватывающая теорию, методы и технические средства определения дефектов в материале контролируемых объектов, в частности в материале деталей машин и элементов металлоконструкций.
Дефектоскопия является составной частью диагностики технического состояния оборудования и его составных частей. Работы, связанные с выявлением дефектов в материале элементов оборудования, совмещаются с ремонтами и техническим обслуживаниями или выполняются самостоятельно в период технического осмотра.
Для выявления скрытых дефектов в конструкционных материалах используются различные методы неразрушающего контроля (дефектоскопии).
Известно, что дефекты в металле являются причиной изменения его физических характеристик: плотности, электропроводности, магнитной проницаемости, упругих и других свойств. Исследование этих характеристик и обнаружение с их помощью дефектов составляет физическую сущность методов неразрушающего контроля. Эти методы основаны на использовании проникающих излучений рентгеновских и гамма-лучей, магнитных и электромагнитных полей, колебаний, оптических спектров, явлений капиллярности и других.
Согласно ГОСТ 18353 методы неразрушающего контроля классифицируют по видам: акустические, магнитные, оптические, проникающими веществами, радиационные, радиоволновые, тепловые, электрические, электромагнитные. Каждый вид представляет собой условную группу методов, объединенных общностью физических характеристик.
Выбор вида дефектоскопии зависит от материала, конструкции и размеров деталей, характера выявляемых дефектов и условий дефектоскопии (в мастерских или на машине). Основными качественными показателями методов дефектоскопии являются чувствительность, разрешающая способность, достоверность результатов. Чувствительность – наименьшие размеры выявляемых дефектов; разрешающая способность – наименьшее расстояние между двумя соседними минимальными выявляемыми дефектами, измеряется в единицах длины или числом линий на 1 мм (мм -1). Достоверность результатов – вероятность пропуска дефектов или браковки годных деталей.
Акустические методы основаны на регистрации параметров упругих колебаний, возбужденных в исследуемом объекте. Эти методы широко применяются для контроля толщины деталей, оплошности (трещин, пористости, раковин и т. п.) и физико-механических свойств (зернистости, межкристаллитной коррозии, глубины закаленного слоя и др.) материала. Контроль выполняется на основании анализа характера распространения звуковых волн в материале детали (амплитуды, фазы, скорости, угла преломления, резонансных явлений). Метод пригоден для деталей, материал которых способен упруго сопротивляться деформациям сдвига (металлы, фарфор, оргстекло, некоторые пластмассы).
В зависимости от частоты акустические волны подразделяют на инфракрасные – с частотой до 20 Гц, звуковые (от 20 до 2∙10 4 Гц), ультразвуковые (от 2∙10 4 до 10 9 Гц) и гиперзвуковые (свыше 10 9 Гц). Ультразвуковые дефектоскопы работают с УЗК от 0,5 до 10 МГц.
К основным недостаткам ультразвуковых методов относятся необходимость достаточно высокой чистоты поверхности деталей и существенная зависимость качества контроля от квалификации оператора-дефектоскописта.
Магнитные методы основаны на регистрации магнитных полей рассеивания над дефектами или магнитных свойств контролируемого объекта. Их применяют для обнаружения поверхностных и подповерхностных дефектов в деталях различной формы, изготовленных из ферромагнитных материалов.
При магнитопорошковом способе для обнаружения магнитного потока рассеивания используют магнитные порошки (сухой способ) или их суспензии (мокрый способ). Проявляющийся материал наносят на поверхность изделия. Под действием магнитного поля рассеивания частицы порошка концентрируются около дефекта. Форма его скоплений соответствует очертанию дефекта.
Сущность магнитографического метода заключается в намагничивании изделия при одновременной записи магнитного поля на магнитную ленту, которой покрывают деталь, и последующей расшифровке полученной информации.
Магнитные силовые линии результирующего поля направлены по винтовым линиям к поверхности изделия, что позволяет обнаруживать дефекты разной направленности.
После контроля все детали, кроме бракованных, размагничивают. Восстановление неразмагниченных деталей механической, обработкой может привести к повреждению рабочих поверхностей из-за притягивания стружки. Не следует размагничивать детали, подвергающиеся при восстановлении нагреву сварочно-наплавочными и другими способами до температуры 600…700 о С.
Степень размагниченности контролируют, осыпая детали стальным порошком. У хорошо размагниченных деталей порошок не должен удерживаться на поверхности. Для этих же целей применяют приборы, снабженные феррозондовыми полюсоискателями.
Для контроля деталей магнитопорошковым способом серийно выпускают стационарные, переносные и передвижные дефектоскопы. Последние включают в себя: источники тока, устройства для подвода тока, намагничивания деталей и для нанесения магнитного порошка или суспензии, электроизмерительную аппаратуру. Стационарные приборы характеризуются большой мощностью и производительностью. На них можно проводить все виды намагничивания.
Вихретоковые методы основаны на анализе взаимодействие внешнего электромагнитного поля с электромагнитным полем вихревых токов, наводимых возбуждающей катушкой в электропроводящем объекте.
Методы вихревых токов позволяют обнаруживать поверхностные дефекты, в том числе под слоем металлических и неметаллических покрытий, контролировать размеры покрытий и деталей (диаметры шаров, труб, проволоки, толщину листов и др.), определять физико-механические свойства материалов (твердости, структуры, глубины азотирования и др.), измерять вибрации и перемещения деталей в процессе работы машины.
Дефектоскопия деталей радиационными методами основана на регистрации ослабления интенсивности радиоактивного излучения при прохождении через контролируемый, объект. Наиболее часто применяются рентгеновский и γ-контроль деталей и сварных швов. Промышленностью выпускаются как передвижные рентгеновские аппараты для работы в условиях мастерских, так и портативные для работы в полевых условиях. Регистрация результатов радиационного контроля осуществляется визуально (изображение на экранах, в том числе стереоскопическое изображение), в виде электрических сигналов, фиксацией на фотопленке или обычной бумаге (ксерорадиография).
Достоинства радиационных методов: высокое качество контроля, особенно литья, сварных швов, состояния закрытых полостей элементов машин; возможность документального подтверждения результатов контроля, не требующего дополнительной расшифровки. Существенными недостатками являются сложность аппаратуры и организации выполнения работ, связанной с обеспечением безопасного хранения и использования источников радиационного излучения.
Радиоволновые методы основаны на регистрации изменения электромагнитных колебаний, взаимодействующих с контролируемым объектом. На практике получили распространение сверхвысокочастотные (СВЧ) методы в диапазоне длин волн от 1 до 100 мм. Взаимодействие радиоволн с объектом оценивают по характеру поглощения, дифракции, отражения, преломления волны, интерференционным процессам, резонансным эффектам. Эти методы применяют для контроля качества и геометрических параметров изделий из пластмасс, стеклопластиков, термозащитных и теплоизоляционных материалов, а также для измерения вибрации.
Тепловые методы. В тепловых методах в качестве диагностируемого параметра используется тепловая энергия, распространяющаяся в объекте, излучаемая объектом, поглощаемая объектом. Температурное поле поверхности объекта является источником информации об особенностях процессов теплопередачи, которые, в свою очередь, зависят от наличия внутренних и наружных дефектов, охлаждения объекта или его части в результате истечения среды и т.п.
Контроль температурного поля осуществляют с помощью термометров, термоиндикаторов, пирометров, радиометров, инфракрасных микроскопов, тепловизоров и других средств.
Оптические методы. Оптический неразрушающий контроль основан на анализе взаимодействия оптического излучения с объектом. Для получения информации используют явления интерференции, дифракции, поляризации, преломления, отражения, поглощения, рассеивания света, а также изменение характеристик самого объекта исследования в результате эффектов фотопроводимости, люминесценции, фотоупругости и других.
К числу дефектов, обнаруживаемых оптическими методами, относятся нарушения сплошности, расслоения, поры, трещины, включения инородных тел, изменения структуры материалов, коррозионные раковины, отклонение геометрической формы от заданной, а также внутренние напряжения в материале.
Визуальная энтроскопия позволяет обнаружить дефекты на поверхностях объекта. Энтроскопы (видеобороскопы) для внутреннего обследования труднодоступных мест объекта включают в себя зонд из стекловолокна, с помощью которого исследователь может проникать вовнутрь объекта, и экран визуального наблюдения поверхности, а также принтер для видеозаписи исследуемой поверхности объекта. Применение оптических квантовых генераторов (лазеров) позволяет расширить границы традиционных оптических методов контроля и создать принципиально новые методы оптического контроля: голографические, акустооптические.
Капиллярный метод дефектоскопии основан на капиллярном проникновении индикаторных жидкостей в полости поверхностных и сквозных несплошностей объекта, и регистрации образующихся индикаторных следов визуально или с помощью преобразователя (датчика).
Капиллярные методы применяют для обнаружения дефектов в деталях простой и сложной формы. Эти методы позволяют обнаруживать дефекты производственно-технологического и эксплуатационного происхождения: трещины шлифовочные, термические, усталостные, волосовины, закаты и др. В качестве проникающих веществ используют керосин, цветные, люминесцентные и радиоактивные жидкости, а также применяют метод избирательно фильтрующихся частиц.
При использовании цветных жидкостей индикаторный рисунок получается цветным, обычно красным, который хорошо выделяется на белом фоне проявителя – цветная дефектоскопия. При использовании люминесцирующих жидкостей индикаторный рисунок становятся хорошо видимым под воздействием ультрафиолетовых лучей – люминесцентный метод. Контроль характера индикаторных рисунков осуществляется визуально-оптическим методом. При этом линии рисунка обнаруживаются сравнительно легко, так как они в десятки раз шире и контрастнее, чем дефекты.
Простейшим примером капиллярной дефектоскопии является керосиновая проба. Проникающей жидкостью служит керосин. Проявитель – мел в виде сухого порошка или водной суспензии. Керосин, просачиваясь в слой мела, вызывает его потемнение, которое обнаруживается при дневном свете.
Достоинствами капиллярной дефектоскопии являются универсальность в отношении формы, и материалов деталей, хорошая наглядность результатов, простота и низкая стоимость материалов, высокая достоверность и хорошая чувствительность. В частности, минимальные размеры обнаруживаемых трещин составляют: ширина 0,001 – 0,002 мм, глубина 0,01 – 0,03 мм. Недостатки: возможность обнаружения только поверхностных дефектов, большая длительность процесса (0,5 м – 1,5 ч) и трудоемкость (необходимость тщательной очистки), токсичность некоторых проникающих жидкостей, недостаточная надежность при отрицательных температурах.
Трещины в деталях можно обнаруживать с помощью керосиновой пробы.
Керосин обладает хорошей смачивающей способностью, глубоко проникает в сквозные дефекты диаметром более 0,1 мм. При контроле качества сварных швов на одну из поверхностей изделия наносят керосин, а на противоположную – адсорбирующее покрытие (350...450 г суспензии молотого мела на 1 л воды). Наличие сквозной трещины определяют по желтым пятнам керосина на меловой обмазке.
Для выявления сквозных пор и трещин широко используются гидравлический и пневматический методы испытаний.
При гидравлическом методе внутреннюю полость изделия заполняют рабочей жидкостью (водой), герметизируют, создают насосом избыточное давление и выдерживают деталь некоторое время. Наличие дефекта устанавливают визуально по появлению капель воды или отпотеванию наружной поверхности.
Пневматический метод нахождения сквозных дефектов более чувствителен, чем гидравлический, так как воздух легче проходит через дефект, чем жидкость. Во внутреннюю полость деталей закачивают сжатый воздух, а наружную поверхность покрывают мыльным раствором или погружают деталь в воду. О наличии дефекта судят по выделению пузырьков воздуха. Давление воздуха, закачиваемого во внутренние полости, зависит от конструктивных особенностей деталей и обычно равно 0,05 – 0,1 МПа.
Методы неразрушающего контроля не являются универсальными. Каждый из них может быть использован наиболее эффективно для обнаружения определенных дефектов. Выбор метода неразрушающего контроля определяется конкретными требованиями практики и зависит от материала, конструкции исследуемого объекта, состояния его поверхности, характеристики дефектов, подлежащих обнаружению, условий работы объекта, условий контроля и технико-экономических показателей.
Поверхностные и подповерхностные дефекты в ферромагнитных сталях обнаруживают намагничиванием детали и фиксацией при этом поля рассеивания с помощью магнитных методов. Те же дефекты в изделиях, изготовленных из немагнитных сплавов, например, жapoпpoчныx, нержавеющих, нельзя выявить магнитными методами. В этом случае применяют, например, электромагнитный метод. Однако и этот метод непригоден для изделий из пластмасс. В этом случае оказывается эффективным капиллярный метод. Ультразвуковой метод малоэффективен при выявлении внутренних дефектов в литых конструкциях и сплавах с высокой степенью анизотропии. Такие конструкции контролируют с помощью рентгеновских или гамма лучей.
Конструкция (форма и размеры) деталей также обусловливает вы-
бор метода контроля. Если для контроля объекта простой формы можно применить почти все методы, то для контроля объектов сложной формы применение методов ограничено. Объекты, имеющие большое количество выточек, канавок, уступов, геометрических переходов, трудно контролировать такими методами, как магнитный, ультразвуковой, радиационный. Крупногабаритные объекты контролируют по частям, определяя зоны наиболее опасных участков.
Состояние поверхности изделия, под которым подразумевают ее шероховатость и наличие на ней защитных покрытий и загрязнений существенно влияет на выбор метода и подготовку поверхности к исследованиям. Грубая шероховатая поверхность исключает применение капиллярных методов, метода вихревых токов, магнитных и ультразвуковых методов в контактном варианте. Малая шероховатость расширяет возможности методов дефетоскопии. Ультразвуковой и капиллярный методы применяют при шероховатости поверхности не более 2,5 мкм, магнитный и вихретоковый – не более 10 мкм. Защитные покрытия не позволяют применять оптические, магнитные и капиллярные методы. Эти методы можно применять только после удаления покрытия. Если такое удаление невозможно, применяют радиационные, и ультразвуковые методы. Электромагнитным методом обнаруживают трещины на деталях, имеющих лакокрасочные и другие неметаллические покрытия толщиной до 0,5 мм и неметаллические немагнитные покрытия до 0,2 мм.
Дефекты имеют различное происхождение и отличаются по виду, размерам, месту расположения, ориентации относительно волокна металла. При выборе метода контроля следует изучить характер возможных дефектов. По расположению дефекты могут быть внутренними, залегающими на глубине более 1 мм, подповерхностными (на глубине до 1 мм) и поверхностными. Для обнаружения внутренних дефектов в стальных изделиях используют чаще радиационный и ультразвуковые методы. Если изделия имеют сравнительно небольшую толщину, a дефекты, подлежащие выявлению, достаточно большие размеры, то лучше пользоваться радиационными методами. Если толщина изделия в направлении просвечивания больше 100-150 мм или требуется обнаружить в нем внутренние дефекты в виде трещин или тонких расслоений, то применять радиационные методы нецелесообразно, так как лучи не приникают на такую глубину и их направление перпендикулярно направлению трещин. В таком случае наиболее приемлем ультразвуковой контроль.
Дефектоскопия – это область знаний, охватывающая теорию, методы и технические средства определения дефектов в материале контролируемых объектов, в частности в материале деталей машин и элементов металлоконструкций.
Дефектоскопия является составной частью диагностики технического состояния оборудования и его составных частей. Работы, связанные с выявлением дефектов в материале элементов оборудования, совмещаются с ремонтами и техническим обслуживанием или выполняются самостоятельно в период технического осмотра. Для выявления скрытых дефектов в конструкционных материалах используются различные методы неразрушающего контроля (дефектоскопии).
Известно, что дефекты в металле являются причиной изменения его физических характеристик: плотности, электропроводности, магнитной проницаемости, упругих и других свойств. Исследование этих характеристик и обнаружение с их помощью дефектов составляет физическую сущность методов неразрушающего контроля. Эти методы основаны на использовании проникающих излучений рентгеновских и гамма-лучей, магнитных и электромагнитных полей, колебаний, оптических спектров, явлений капиллярности и других.
Согласно ГОСТ 18353 методы неразрушающего контроля классифицируют по видам: акустические, магнитные, оптические, проникающими веществами, радиационные, радиоволновые, тепловые, электрические, электромагнитные. Каждый вид представляет собой условную группу методов, объединенных общностью физических характеристик.
Выбор вида дефектоскопии зависит от материала, конструкции и размеров деталей, характера выявляемых дефектов и условий дефектоскопии (в мастерских или на машине). Основными качественными показателями методов дефектоскопии являются чувствительность, разрешающая способность, достоверность результатов. Чувствительность – наименьшие размеры выявляемых дефектов; разрешающая способность – наименьшее расстояние между двумя соседними минимальными выявляемыми дефектами, измеряется в единицах длины или числом линий на 1 мм (мм –1). Достоверность результатов – вероятность пропуска дефектов или браковки годных деталей.
Акустические методы основаны на регистрации параметров упругих колебаний, возбужденных в исследуемом объекте. Эти методы широко применяются для контроля толщины деталей, сплошности (трещин, пористости, раковин и т.п.) и физико-механических свойств (зернистости, межкристаллитной коррозии, глубины закаленного слоя и др.) материала. Контроль выполняется на основании анализа характера распространения звуковых волн в материале детали (амплитуды, фазы, скорости, угла преломления, резонансных явлений). Метод пригоден для деталей, материал которых способен упруго сопротивляться деформациям сдвига (металлы, фарфор, оргстекло, некоторые пластмассы).
Акустические методы подразделяют на активные, основанные на излучении и приеме волн (теневой, резонансный, эхо-импульсный, велосимметрический методы), и пассивные, основанные на приеме колебаний волн исследуемого объекта (акустической эмиссии, виброшумодиагностические методы).
На ремонтных предприятиях нефтегазовой отрасли широко применяют ультразвуковую дефектоскопию. Сущность ее заключается в способности ультразвуковых колебаний приникать вглубь материала контролируемого изделия и отражаться от дефектов, являющихся нарушением сплошности материала.
Ультразвуковыми колебаниями принято называть упругие механические колебания с частотой более 20 кГц. Для излучения и приема ультразвуковых колебаний обычно используют пьезоэлектрические преобразователи-пластинки, изготовленные из монокристаллов кварца, сульфата лития и других материалов.
При внесении пьезоэлемента в электрическое поле в нем возникают упругие деформации, величина и направление которых зависят от параметров электрического поля. Указанный процесс является строго обратимым, т.е. если на пьезоэлемент действует переменное напряжение, изменяющееся по определенному закону, то и возникающее электрическое напряжение подчиняется этому же закону. Подобное явление называется пьезоэлектри-ческим эффектом.
Ультразвуковые колебания распространяются в виде узких направленных пучков. Они могут отражаться, преломляться и фокусироваться. При падении на границу раздела двух фаз, обладающих различным акустическим сопротивлением, в том числе нарушенной сплошности материала (трещин, раковин, расслоений и др.), часть ультразвуковых колебаний отражается, причем угол падения равен углу отражения, а остальная часть УЗК проходит во вторую среду, преломляясь в ней. Направленность УЗК и способность их отражаться от границы раздела двух сред используются для выявления в материалах трещин, расслоений, пор, газовых и шлаковых включений и измерения толщины деталей.
Ультразвуковая дефектоскопия осуществляется тремя основными методами: теневым, резонансным и эхо-методом.
Теневой метод основан на появлении за дефектом «звуковой тени» при прохождении ультразвука через деталь, помещенную между излучателем колебаний и приемным устройством. На рис. 7.8 изображена схема дефектоскопа, работающего по принципу теневого метода. Высокочастотные электрические колеба-
Рис. 7.8. Схема ультразвукового дефектоскопа, работающего по теневому методу:
а – без дефекта; б – с дефектом; 1 – генератор; 2 – преобразователь пьезоэлектрический; 3 – контролируемая деталь; 4 – ультразвуковые колебания; 5 – преобразователь приемный пьезоэлектрический; 6 – дефект; 7 – прибор регистрирующий
ния, вырабатываемые генератором 1 , подаются на пьезоэлектрический преобразователь 2 , в котором преобразуются в механические колебания ультразвуковой частоты. При плотном соприкосновении преобразователя 2 3 колебания (волны) 4 распространяются вглубь материала детали, достигают при отсутствии дефекта приемного пьезоэлектрического преобразователя 5 и регистрируются прибором 7 . Если на пути ультразвуковых колебаний встречается дефект 6 , то они отражаются от него и не попадают на приемный преобразователь 5 , т.е. за дефектом образуется «звуковая тень». При этом на регистрирующем приборе 7 отсутствуют показания, что свидетельствует о наличии дефекта.
Применяются также временной теневой и зеркально-теневой методы.
Временной теневой метод основан на запаздывании импульса, вызванного огибанием дефекта.
Зеркально-теневой метод основан на ослаблении сигнала, отраженного от противоположной поверхности изделия (донный эффект).
Резонансный метод основан на возникновении стоячих волн в материале контролируемой детали при совпадении частоты колебаний, создаваемых в детали внешним источником, с частотой собственных колебаний детали. Резонансным методом выявляют коррозионные раковины, расслоения в металле и другие повреждения.
Наибольшее применение для контроля материала деталей получил импульсный эхо-метод , основанный на принципе посылки в материал контролируемой детали ультразвуковых колебаний и приеме отраженных волн.
На рис. 7.9 приведена блок-схема импульсного эхо-дефек-тоскопа. Импульсы электромагнитных колебаний определен- ной частоты, вырабатываемые импульсным генератором 6
, поступают на пьезоэлектрический преобразователь 3
искательной головки, который под их действием деформируется и излучает упругие механические колебания ультразвуковой частоты. При соприкосновении пьезоэлектрического преобразователя 3
с поверхностью контролируемой детали 1
через слой контактной смазки ультразвуковые колебания распространяются внутрь материала детали и, достигнув противоположной стороны детали или дефекта 8
, отражаются от них. Отраженные импульсы поступают на приемный пьезоэлектрический преобразователь 2
, находящийся в той же искательной головке, где вновь преобразуются в электрические сигналы, которые, пройдя через усилитель 4
, поступают на электронно-лучевую трубку 5
. Одновременно с пуском импульсного генератора 6
включается генератор основной развертки 7
, который предназначен для получения на экране электронно-лучевой трубки горизонтальной развертки луча во времени.
Таким образом, на экране электронно-лучевой трубки фиксируются колебания основной развертки, слившиеся в одну сплошную горизонтальную линию, и пики эхо-сигналов – от поверхности входа в исследуемый материал (начальный импульс), от дефекта и от противоположной поверхности детали (донный импульс). Расстояния l
1 и l
2 , на которых расположены импульс дефекта и донный импульс по отношению к начальному импульсу соответствуют глубине залегания дефекта и толщине изделия. По амплитуде эхо-сигнала, отраженного от дефекта, судят о размере дефекта.
Окончательное заключение о координатах, форме и размерах дефекта, например, трещины, дается после его прозвучивания по нормали к поверхностям детали и под различными углами к ним (рис. 7.10). Амплитуда эхо-сигнала будет наибольшей, когда импульсы ультразвуковых колебаний направлены по нормали к поверхности дефекта (поз. а ). По мере увеличения угла a между нормалью к поверхности дефекта и направлением импульсов ультразвуковых колебаний амплитуда эхо-сигнала уменьшается (поз. b ) и примет нулевое значение, когда направление импульсов и трещины совпадут (поз. с ). Если отражающая поверхность дефекта достаточно велика, то по форме огибающей эхо-сигнала, наблюдаемого на экране электронно-лучевой трубки, можно судить о расположении трещины в материале.
Искательные головки (рис. 7.11) разделяют на три типа: прямые, наклонные и раздельно-совмещенные. Первые предназначены для ввода в изделие продольных звуковых волн, перпендикулярных к поверхности изделия, вторые – для ввода в изделие комбинаций УЗК с преобладанием (в зависимости от поставленной цели) поверхностных, продольных или поперечных волн и третьи – для ввода пучка продольных волн под определенным углом к плоскости, перпендикулярной к поверхности детали.
Тип волны зависит от угла ввода, который может изменяться. Применение таких головок дает возможность обнаруживать не только внутренние дефекты, но и наружные, например, усталостные трещины различного характера.
Основным элементом всех искательных головок служит пье-зопластина. Ее толщина равна половине длины волны излучаемых ультразвуковых колебаний.
Перед выполнением дефектоскопии поверхности детали, по которым производится контроль, должны быть очищены от загрязнений. Чтобы обеспечить надежный акустический контакт искательной головки с поверхностью детали без воздушных промежутков, на поверхность детали, контактирующую с искательной головкой, наносят слой масла. Чем больше криволинейность поверхности и выше температура, тем более вязкие масла следует применять в качестве контактной жидкости.
Дефектоскопию цилиндрических и конических, наружных и внутренних резьб бурильных и эксплуатационных труб и
Современные ультразвуковые дефектоскопы обладают высокой чувствительностью и точностью до 2 %.
К основным недостаткам ультразвуковых методов относятся необходимость достаточно высокой чистоты поверхности деталей и существенная зависимость качества контроля от квалификации оператора-дефектоскописта.
Магнитные методы основаны на регистрации магнитных полей рассеивания над дефектами или магнитных свойств контролируемого объекта. Их применяют для обнаружения поверхностных и подповерхностных дефектов в деталях различной формы, изготовленных из ферромагнитных материалов.
Магнитный поток, встречая на своем пути дефект с низкой магнитной проницаемостью по сравнению с ферромагнитным материалом детали, огибает его. Часть магнитных силовых линий выходит за пределы детали (рис. 7.15), образуя поле рассеива-
ния. Наличие последнего, а следовательно и дефекта, обнаруживают различными методами (магнитопорошковый, магнитографический и феррозондовый).
При магнитопорошковом способе для обнаружения магнитного потока рассеивания используют магнитные порошки (сухой способ) или их суспензии (мокрый способ). Проявляющийся материал наносят на поверхность изделия. Под действием магнитного поля рассеивания частицы порошка концентрируются около дефекта. Форма их скоплений соответствует очертанию дефекта (рис. 7.16).
Сущность магнитографического метода заключается в намагничивании изделия при одновременной записи магнитного поля на магнитную ленту, которой покрывают деталь, и последующей расшифровке полученной информации.
Для обнаружения дефектов феррозондовым способом применяют феррозондовые преобразователи.
При контроле деталей, поступающих в ремонт, наиболее распространен магнитопорошковый способ. Технология определения дефекта состоит из следующих операций: очистки детали от загрязнений; подготовки суспензии (мокрым способом); намагничивания контролируемой детали; осмотра поверхности детали с целью выявления мест, покрытых отложениями порошка; размагничивания детали.
Намагниченность деталей должна быть достаточной для создания около дефекта магнитного поля рассеивания, способного притягивать и удерживать частицы порошка. Через детали пропускают электрический ток или помещают их в магнитное поле соленоида. Различают три способа намагничивания: полюсное, циркулярное и комбинированное.
Полюсным намагничиванием создают продольное магнитное поле (вдоль детали). Деталь помещают между полюсами электромагнита (постоянного магнита) или в магнитное поле соленоида. Это намагничивание применяют для выявления дефектов, расположенных перпендикулярно к продольной оси детали или под углом к ней не более 20–25°.
Циркулярным намагничиванием создают магнитное поле, магнитные силовые линии которого расположены в виде замкнутых концентрических окружностей. Через деталь пропускают электрический ток. При необходимости обнаружения дефекта на внутренней цилиндрической поверхности ток пропускают через стержень или кабель из немагнитного материала (медь, латунь, алюминий), помещенный в отверстие детали. Это намагничивание служит для нахождения дефектов, расположенных вдоль продольной оси детали или под небольшим углом к ней.
Комбинированное намагничивание заключается в одновременном воздействии на деталь двух взаимно перпендикулярных магнитных полей. В результате их сложения образуется результирующее магнитное поле, величина и направление которого зависят от вектора магнитной напряженности каждого из слагаемых. Для получения комбинированного магнитного поля обычно через деталь пропускают электрический ток, создавая в ней циркулярное магнитное поле, и одновременно помещают в соленоид (или электромагнит), создавая продольное магнитное поле.
Магнитные силовые линии результирующего поля направлены по винтовым линиям к поверхности изделия, что позволяет обнаруживать дефекты разной направленности.
Вихретоковые методы основаны на анализе взаимодействия внешнего электромагнитного поля с электромагнитным полем вихревых токов, наводимых возбуждающей катушкой в электропроводящем объекте.
Контроль методами вихревых токов базируется на зависимостях параметров (амплитуды, фазы, переходных характеристик и др.) вихревых токов, возбуждаемых в детали, от ее формы, размеров, сплошности и физико-механических свойств материала. Возбудителями вихревых токов могут служить переменное поле тока в проводе, движущиеся магниты, волны радиоизлучения. Для контроля деталь или ее часть помешается в переменный магнитный поток F 0 напряженностью Н 0 (рис. 7.17). Под действием магнитного потока в детали возбуждаются вихревые токи плотностью d, создающие вторичный встречный магнитный поток F в напряженностью Н в. Исследуя параметры потока F в при известных параметрах первичного потока F 0 , можно судить о качественных показателях деталей.
Методы вихревых токов позволяют обнаруживать поверхностные дефекты, в том числе под слоем металлических и неметаллических покрытий, контролировать размеры покрытий и деталей (диаметры шаров, труб, проволоки, толщину листов и др.), определять физико-механические свойства материалов (твердость, структуру, глубину азотирования и др.), измерять вибрации
Рис.7.17. Схема контроля методом вихревых токов
и перемещения деталей в процессе работы машины. Не всегда требуется непосредственный контакт датчика с исследуемой деталью, возможен контроль при одностороннем доступе (измерение толщины листов коробчатых конструкций и т.п.). Методы пригодны для контроля деталей из немагнитных металлов (по значению электропроводности). Важным преимуществом этих методов является автономность и портативность приборов, любой вид индикации, хорошая приспособленность к автоматизации. Контроль методами вихревых токов отличается хорошей точностью, а в случае выявления поверхностных трещин обеспечивает очень высокую чувствительность: минимальная ширина раскрытия трещины 0,0005–0,001 мм, глубина 0,15–0,2 мм. Для выявления трещин отечественной промышленностью выпускаются портативные дефектоскопы. Их чувствительность несколько ниже.
Недостатками рассматриваемых методов являются сравнительная сложность оборудования, необходимость в высокой квалификации персонала для обслуживания, использования и анализа результатов контроля. Приборы контроля, выпускаемые промышленностью, являются узкоспециализированными по видам контроля и материалам, что сдерживает их широкое применение.
Дефектоскопия деталей радиационными методами
Дефектоскопия деталей радиационными методами
основана на регистрации ослабления интенсивности радиоактивного излучения при прохождении через контролируемый объект. Схема просвечивания детали радиационными лучами представлена на рис. 7.18. Наиболее часто применяются рентгеновский и g-контроль деталей и сварных швов. Промышленностью выпускаются как передвижные рентгеновские аппараты для работы в условиях мастерских, так и портативные для работы в полевых условиях. Для работы вблизи взрыво- и пожароопасных объектов, при отсутствии на месте работ электроэнергии или при ограниченном доступе к объекту контроля (например, при работе на машинах) вместо рентгеновских используются гамма-дефектоскопы. Некоторые дефектоскопы снабжаются шлангом-ампулопроводом для подачи источника излучения из радиационной головки в труднодоступные места на расстояние до 12 м.
Регистрация результатов радиационного контроля осуществляется визуально (изображение на экранах, в том числе стереоскопическое изображение) в виде электрических сигналов, фиксацией на фотопленке или обычной бумаге (ксерорадио-графия).
Достоинства радиационных методов – высокое качество контроля, особенно литья, сварных швов, состояния закрытых полостей элементов машин; возможность документального подтверждения результатов контроля, не требующего дополнительной расшифровки. Существенными недостатками являются сложность аппаратуры и организации выполнения работ, связанной с обеспечением безопасного хранения и использования источников радиационного излучения.
Радиоволновые методы основаны на регистрации изменения электромагнитных колебаний, взаимодействующих с контролируемым объектом. На практике получили распространение сверхвысокочастотные (СВЧ) методы в диапазоне длин волн от 1 до 100 мм. Взаимодействие радиоволн с объектом оценивают по характеру поглощения, дифракции, отражения, преломления волны, интерференционным процессам, резонансным эффектам. Эти методы применяют для контроля качества и геометрических параметров изделий из пластмасс, стеклопластиков, термозащитных и теплоизоляционных материалов, а также для измерения вибрации.
Тепловые методы. В тепловых методах в качестве диагностируемого параметра используется тепловая энергия, распространяющаяся в объекте, излучаемая объектом, поглощаемая объектом. Температурное поле поверхности объекта является источником информации об особенностях процессов теплопередачи, которые, в свою очередь, зависят от наличия внутренних и наружных дефектов, охлаждения объекта или его части в результате истечения среды и т.п.
Различают пассивные и активные методы теплового контроля. При пассивном контроле анализ тепловых полей производят в процессе их естественного возникновения. При активном – нагрев производят внешним источником тепловой энергии.
Контроль температурного поля осуществляют с помощью термометров, термоиндикаторов, пирометров, радиометров, инфракрасных микроскопов, тепловизоров и других средств.
Тепловизионная аппаратура, получившая в настоящее время широкое применение в диагностике, основана на сканировании поверхности объекта лучом инфракрасного спектра, приеме, усилении и развертке отраженного луча. В технической диагностике приборы термовидения с дистанционным обследованием объекта применяют:
при контроле качества изоляции, футеровки;
при контроле напряженного состояния металла.
Оптические методы. Оптический неразрушающий контроль основан на анализе взаимодействия оптического излучения с объектом. Для получения информации используют явления интерференции, дифракции, поляризации, преломления, отражения, поглощения, рассеивания света, а также изменение характеристик самого объекта исследования в результате эффектов фотопроводимости, люминесценции, фотоупругости и других.
Оптическое излучение или свет – электромагнитное излучение с длиной волн от 10 –5 до 103 мкм, в котором принято вы-делять ультрафиолетовую (от 10 –3 до 0,38 мкм), видимую (от 0,38 до 0,78 мкм) и инфракрасную (от 0,78 до 103 мкм) области спектра.
К числу дефектов, обнаруживаемых оптическими методами, относятся нарушения сплошности, расслоения, поры, трещины, включения инородных тел, изменения структуры материалов, коррозионные раковины, отклонение геометрической формы от заданной, а также внутренние напряжения в материале.
Применение переносных микроскопов дает возможность исследовать состояние и структуру поверхности материалов при увеличении. В сочетании со стробоскопом оптические методы позволяют исследовать подвижные детали.
Визуальная энтроскопия позволяет обнаружить дефекты на поверхностях объекта. Энтроскопы для внутреннего обследования труднодоступных мест объекта включают зонд из стекловолокна, с помощью которого исследователь может проникать внутрь объекта, и экран визуального наблюдения поверхности, а также принтер для видеозаписи исследуемой поверхности объекта. Применение оптических квантовых генераторов (лазеров) позволяет расширить границы традиционных оптических методов контроля и создать принципиально новые методы оптического контроля: голографические, акустооптические.
Капиллярный метод дефектоскопии основан на капиллярном проникновении индикаторных жидкостей в полости поверхностных и сквозных несплошностей объекта и регистрации образующихся индикаторных следов визуально или с помощью преобразователя (датчика).
Капиллярные методы применяют для обнаружения дефектов в деталях простой и сложной формы. Эти методы позволяют обнаруживать дефекты производственно-технологического и эксплуатационного происхождения – трещины шлифовочные, термические, усталостные, волосовины, закаты и др. В качестве проникающих веществ используют керосин, цветные, люминесцентные и радиоактивные жидкости, а также применяют метод избирательно фильтрующихся частиц.
Схема контроля деталей капиллярными методами приведена на рис. 7.19. Очищенная от грязи и специальных покрытий (краска, гальванические покрытия и др.) деталь 1
покрывается проникающей жидкостью 2
(рис. 7.19, а
). Ускорение заполнения жидкостью дефектов достигается в зависимости от ее свойств подогревом (жидкости или детали), созданием вакуума или компрессии, упругим деформированием или воздействием ультразвуком. Затем жидкость с поверхности удаляют протиркой ветошью, промывкой или продувкой (рис. 7.19, б
) и в зону контроля кистью или краскораспылителем наносят равномерный слой проявителя. Он поглощает оставшуюся в полостях дефектов жидкость, образуя индикаторный рисунок дефектов (рис. 7.19, в
), а также создает фон, улучшающий видимость рисунка.
При использовании цветных жидкостей индикаторный рисунок получается цветным, обычно красным, который хорошо выделяется на белом фоне проявителя – цветная дефектоскопия. При использовании люминесцирующих жидкостей индикаторный рисунок становится хорошо видимым под воздействием ультрафиолетовых лучей – люминесцентный метод. Контроль характера индикаторных рисунков осуществляется визуально-оптическим методом. При этом линии рисунка обнаруживаются сравнительно легко, так как они в десятки раз шире и контрастнее, чем дефекты.
Простейшим примером капиллярной дефектоскопии является керосиновая проба. Проникающей жидкостью служит керосин. Проявитель – мел в виде сухого порошка или водной суспензии. Керосин, просачиваясь в слой мела, вызывает его потемнение, которое обнаруживается при дневном свете.
Достоинствами капиллярной дефектоскопии являются универсальность в отношении формы и материалов деталей, хорошая наглядность результатов, простота и низкая стоимость материалов, высокая достоверность и хорошая чувствительность. В частности, минимальные размеры обнаруживаемых трещин составляют: ширина 0,001–0,002 мм, глубина 0,01–0,03 мм. Недостатки: возможность обнаружения только поверхностных дефектов, большая длительность процесса и трудоемкость (необходимость тщательной очистки), токсичность некоторых проникающих жидкостей, недостаточная надежность при отрицательных температурах.
В ремонтном производстве при использовании люминесцентного метода дефектоскопии применяют проникающие жидкости различного состава. Их наносят с помощью пульверизатора, окунанием в раствор илимягкой кистью. После выдержки детали в течение нескольких минут (не более 5) излишки жидкости удаляют, протирая поверхность ветошью, или промывают струей холодной воды под давлением 0,2 МПа с последующей сушкой.
Далее приступают к выявлению дефекта. Чаще всего применяют самопроявляющийся способ, при котором после пропитки и очистки деталь нагревают, что способствует быстрому выходу проникающей жидкости из дефекта и растеканию ее по краям трещины. Затем деталь помещают в дефектоскоп и облучают ультрафиолетовыми лучами. Источником ультрафиолетовых лучей служат ртутно-кварцевые лампы, свет от которых пропускают через светофильтры. Промышленность выпускает переносные и стационарные дефектоскопы.
Трещины в деталях можно обнаруживать с помощью керосиновой пробы. Керосин обладает хорошей смачивающей способностью, глубоко проникает в сквозные дефекты диаметром более 0,1 мм. При контроле качества сварных швов на одну из поверхностей изделия наносят керосин, а на противоположную – адсорбирующее покрытие (350–450 г суспензии молотого мела на 1 л воды). Наличие сквозной трещины определяют по желтым пятнам керосина на меловой обмазке.
Для выявления сквозных пор и трещин широко используются гидравлический и пневматический методы испытаний.
При гидравлическом методе внутреннюю полость изделия заполняют рабочей жидкостью (водой), герметизируют, создают насосом избыточное давление и выдерживают деталь некоторое время. Наличие дефекта устанавливают визуально по появлению капель воды или отпотеванию наружной поверхности.
Пневматический метод нахождения сквозных дефектов более чувствителен, чем гидравлический, так как воздух легче проходит через дефект, чем жидкость. Во внутреннюю полость деталей закачивают сжатый воздух, а наружную поверхность покрывают мыльным раствором или погружают деталь в воду. О наличии дефекта судят по выделению пузырьков воздуха. Давление воздуха, закачиваемого во внутренние полости, зависит от конструктивных особенностей деталей и обычно равно 0,05– 0,1 МПа.
Методы неразрушающего контроля не являются универсальными. Каждый из них может быть использован наиболее эффективно для обнаружения определенных дефектов. Выбор метода неразрушающего контроля определяется конкретными требованиями практики и зависит от материала, конструкции исследуемого объекта, состояния его поверхности, характеристики дефектов, подлежащих обнаружению, условий работы объекта, условий контроля и технико-экономических показателей.
Неразрушающие методы контроля | Материал объекта | Форма объекта | Шероховатость | Место расположения дефекта | Условия контроля | |||||||||
Металл маг-нитный | Металл не-магнитный | Неметалл | Простая (плита, лист, труба) | Сложная | R а > 5 мкм | R а < 5 мкм | На поверх-ностном слое | В подповерх-ностном слое | В глубине металла | Под слоем защитного покрытия | В условиях производст-ва | В условиях эксплуата-ции | При ремонте | |
Теневой Резонансный Эхо-импульсный Велосимметрический Акустической эмиссии Импедансный Свободных колебаний | + + + – + + + | + + + – + + + | + + + + – + + | + + + + + + + | – – + – – – – | + – + – – – + | + + + + + + + | + – + – + – – | + + + + + – – | + + + – + + + | – – + – – – – | + + + + + + + | – – + + + + – | – – + + – – – |
Магнитопорошковый Магнитографический Феррозондовый | + + + | – – – | – – – | + + + | – – – | – + – | + – + | + + + | + + + | – – + | – – – | + + + | + + – | + + + |
Оптический | + | + | + | + | + | + | + | + | – | – | – | + | + | + |
Цветной Люминесцентный Тенеисканием | + + + | + + + | + + + | + + + | + + + | – – + | + + + | + + – | – – – | – – – | – – – | + + + | + – + | + + + |
Рентгенографический Гамма-графический | + + | + + | + + | + + | + + | + + | + + | + + | + + | + + | + + | + + | + + | + + |
Радиоволновый | – | – | + | + | – | – | + | + | + | + | – | + | – | – |
Тепловой | + | + | + | + | – | – | + | + | + | + | – | + | – | – |
Электрический | + | + | + | + | – | – | + | + | + | – | + | + | – | – |
Вихретоковый | + | + | – | + | + | – | + | + | + | – | + | + | + | + |
Похожая информация.
Методы с использованием проникающих сред.
Это - методы для контроля герметичности соединений в резервуарах, газгольдерах, трубопроводах и других подобных сооружениях. Различают методы течеискания и капиллярный.
Методы течеискания.
1. Испытание водой. Ёмкость наполняют водой до отметки, несколько превышающей эксплуатационную, и контролируют состояние швов. В закрытых сосудах давление жидкости можно повысить дополнительным нагнетанием воды или воздуха. Состояние шва можно также проверить сильной струей воды из брандбойта под давлением 1 ат, направленной нормально к поверхности шва.
2. Проба керосином. Благодаря малой вязкости и незначительному по сравнению с водой поверхностному натяжению керосин легко проникает через самые малые поры. Если поверхность шва с одной стороны обильно смочить керосином, а противоположную сторону заранее побелить водным раствором мела, то при наличии дефекта на светлом фоне проявятся характернвые ржавые пятна.
3. Проба сжатым воздухом. Шов с одной стороны обмазывают мыльной водой, а с противоположной обдувают сжатым воздухом под давлением 4 ат.
4. Проба вакуумом. Шов с одной стороны обмазывают мыльной водой. Затем к шву с этой же стороны приставляется металлическая кассета в виде плоской коробки без дна, но окаймленной снизу резиновой прокладкой, с прозрачным верхом. Вакуум-насосом в кассете создается небольшое разряжение.
Капиллярный метод.
На конструкцию наносят специальную жидкость (индикаторный пенетрант), которая под действием капиллярных сил заполняет полости поверхностных дефектов. Затем жидкость удаляют с поверхности конструкции. Если в жидкости был порошок, то он отфильтруется и скопится в дефектах; при использовании жидкости без порошка на конструкцию после удаления жидкости наносится проявитель - мел (в виде порошка или водной суспензии), который реагирует с жидкостью в дефектах и образует индикаторный рисунок высокой цветовой контрастности. При применении реактивов образуются даже рисунки, способные люминисцировать в ультрафиолетовых лучах и при дневном свете.
Акустические методы.
Ультразвуковой метод.
Контроль дефектов производится с помощью сквозного прозвучивания объекта. На участках без дефектов скорость ультразвуковой волны не падает, а на участке с дефектами, содержащими воздух, волна полностью затухает или скорость её заметно уменьшается.
Контроль качества сварных швов стыковых соединенийпроизводится следующим образом. Для обнаружения шлаковых включений, раковин, газовых пор, трещин, непроваров чаще всего применяют эхо-метод, когда источник и приёмник волн совмещены в одном преобразователе (поочередно происходит пуск волны и её приём). Преобразователь - призматический, позволяющий пускать и принимать волну под углом к вертикали. Перемещают преобразователь зигзагообразно вдоль сварного шва. Отражение волны от противоположной грани соединенных сваркой конструктивных элементов (скорость волны, на прямом и обратном пути которой, возможно, встретился дефект) сравнивают с эталонными отражениями (скоростями), полученными на предварительно сваренных эталонных фрагментах соединений с искусственно сделанными дефектами.
Метод акустической эмиссии основан на регистрации акустических волн в металле при его пластическом деформировании.
Регистрируя скорость движения волн, можно обнаружить накопление опасных разрушений (зоны концентрации напряжений) в процессе нагружения конструкций и их эксплуатации. Специальная аппаратура «слышит» треск металла.
Методы с использованием ионизирующих излучений.
Радиографический метод с использованиемрентгеновского или -излучения:
При просвечивании дефект спроецируется на пленку в виде затемненного пятна, по которому можно определить положение дефекта в плане и его величину в направлении, перпендикулярном направлению просвечивания. О величине дефекта в направлении просвечивания судят, сравнивая интенсивность затемнения пятна с интенсивностями затемнений, получившихся на фотопленке от прорезей разной глубины на эталоне чувствительности. Глубину залегания дефекта определяют смещением источника излучения параллельно пленке и пуском потока под новым углом к ней, как это уже описано для бетонных конструкций.
Пуск потока под новым углом преследует еще одну цель: выявить дефекты, вытянутые перпендикулярно первоначальному направлению потока, пересекаемые им по меньшему протяжению и вследствие этого оставшиеся «незамеченными».
Магнитные, электрические и электромагнитные методы.
Магнитные методы основаны на регистрации полей рассеяния над дефектами или на определении магнитных свойств контролируемых изделий. Различают методы: магнитопорошковый, магнитографический, феррозондовый, преобразователя Холла, индукционный и пондеромоторный.
Магнитопорошковый метод. Любая ферромагнитная деталь состоит из очень маленьких самопроизвольно намагниченных областей - доменов. В размагниченном состоянии магнитные поля доменов направлены произвольно и компенсируют друг друга, суммарное магнитное поле доменов равно нулю. Если деталь помещается в намагничивающее поле, то под его влиянием поля отдельных доменов устанавливаются по направлению внешнего поля, образуется результирующее магнитное поле доменов, деталь намагничивается.
Магнитный поток в бездефектной зоне распространяется прямолинейно по направлению результирующего магнитного поля. Если же магнитный поток наталкивается на открытый или скрытый дефект (прослойку воздуха или неферромагнитное включение), то он встречает большое магнитное сопротивление (участок с пониженной магнитной проницаемостью), линии магнитного потока искривляются и часть их выходит на поверхность конструкции. Там, где они выходят из конструкции и входят в неё, возникают местные полюса N, S и магнитное поле над дефектом.
Если намагничивающее поле снять, местные полюса и магнитное поле над дефектом всё равно останутся.
Наибольший возмущающий эффект и наибольшее местное магнитное поле вызовет дефект, ориентированный перпендикулярно направлению линий магнитного потока. Если через исследуемую конструкцию пропустить ток одновременно постоянный и переменный, это позволит создать переменное направление намагничивания и выявить различно ориентированные дефекты.
Для регистрации местных магнитных полей над дефектами применяют мелкоразмолотый железный сурик, окалину и т.п., выбирая цвет порошка контрастным по отношению к цвету предварительно зачищенной поверхности конструкции; порошок наносят сухим (напыление) или в виде суспензии - водной (что предпочтительнее для строительных конструкций) или керосино-масляной. Вследствие намагничивания и притягивания друг к другу частиц порошка, над дефектами он оседает в виде заметных скоплений.
Для регистрации местных магнитных полей (дефектов) в сварных швах используют магнитографический метод. Намагничивание производят соленоидом, витки которого располагают параллельно шву по обеим его сторонам; на шов накладывается магнитная лента (аналогичная применяемой в звукозаписи, но несколько большей ширины). Местное магнитное поле запишется на ленте. Прослушивают запись на звуковом индикаторе.
Феррозондовый метод основан на преобразовании напряженности магнитного поля в электрический сигнал. Перемещая два зонда по поверхности конструкции после её размагничивания, выискивают местные магнитные поля над дефектами; возникающая в этих местах электродвижущая сила зафиксируется прибором.
Эффект Холла заключается в том, что если прямоугольную пластину из полупроводника (германия, антимонита, арсенида индия) поместить в магнитное поле перпендикулярно вектору напряженности и пропустить по ней ток в направлении от одной грани к другой противоположной, то на двух других гранях возникнет электродвижущая сила, пропорциональная напряженности магнитного поля. Размеры пластины 0,7х0,7 мм, толщина 1 мм. Местные магнитные поля над дефектами выискивают, перемещая прибор по конструкции после её размагничивания.
Индукционный метод. Выискивание местных магнитных полей над дефектами в сварных швахпроизводится с помощью катушки с сердечником, которая питается переменным током и является элементом мостовой схемы. Возникающая над дефектом электродвижущая сила усиливается и преобразуется в звуковой сигнал или подаётся на самопишущий прибор или осциллограф.
Пондеромоторный метод. Через рамку прибора протекает электрический ток, образуя магнитное поле вокруг себя. Прибор устанавливают на железнодорожный рельс, подвергаемый намагничиванию внешним магнитным полем. Магнитные поля взаимодействуют друг с другом, рамка поворачивается и занимает какое-то положение. При перемещении по рельсу и обнаружении потока рассеяния над дефектом, рамка меняет первоначальное положение.
Дефектоскопия это область знаний, охватывающая теорию, методы и технические средства определения дефектов в материале контролируемых объектов, в частности в материале деталей машин и элементов металлоконструкций.
Вследствие несовершенства технологии изготовления или в результате эксплуатации в тяжёлых условиях в изделиях появляются различные дефекты - нарушения сплошности или однородности материала, отклонения от заданного химического состава или структуры, а также от заданных размеров. Дефекты изменяют физические свойства материала (плотность, электропровоность, магнитные, упругие свойства и др.). В основе существующих методов Дефектоскопия лежит исследование физических свойств материалов при воздействии на них рентгеновских, инфракрасных, ультрафиолетовых и гамма-лучей, радиоволн, ультразвуковых колебаний, магнитного и электростатического полей и др.
Наиболее простым методом Дефектоскопия является визуальный - невооружённым глазом или с помощью оптических приборов (например, лупы). Для осмотра внутренних поверхностей, глубоких полостей и труднодоступных мест применяют специальные трубки с призмами и миниатюрными осветителями (диоптрийные трубки) и телевизионные трубки. Используют также лазеры для контроля, например качества поверхности тонкой проволоки и др. Визуальная Дефектоскопия позволяет обнаруживать только поверхностные дефекты (трещины, плёны и др.) в металлических изделиях и внутренние дефекты в изделиях из стекла или прозрачных для видимого света пластмасс. Минимальный размер дефектов, обнаруживаемых невооружённым глазом, составляет 0,1-0,2 мм, а при использовании оптических систем - десятки мкм.
Рентгенодефектоскопия основана на поглощении рентгеновских лучей, которое зависит от плотности среды и атомного номера элементов, образующих материал среды. Наличие таких дефектов, как трещины, раковины или включения инородного материала, приводит к тому, что проходящие через материал лучи (рис. 1 ) ослабляются в различной степени. Регистрируя распределение интенсивности проходящих лучей, можно определить наличие и расположение различных неоднородностей материала.
Рис. 1. Схема рентгеновского просвечивания: 1 - источник рентгеновского излучения; 2 - пучок рентгеновских лучей; 3 - деталь; 4 - внутренний дефект в детали; 5 - невидимое глазом рентгеновское изображение за деталью; 6 - регистратор рентгеновского изображения.
Гамма-дефектоскопия(радиоационная) имеет те же физические основы, что и рентгенодефектоскопия, но используется излучение гамма-лучей, испускаемых искусственными радиоактивными изотопами различных металлов (кобальта, иридия, европия и др.). Используют энергию излучения от нескольких десятков кэв до 1-2 Мэв для просвечивания деталей большой толщины. Этот метод имеет существенные преимущества перед рентгенодефектоскопией: аппаратура для гамма-дефектоскопии сравнительно проста, источник излучения компактный, что позволяет обследовать труднодоступные участки изделий. Кроме того, этим методом можно пользоваться, когда применение рентгенодефектоскопии затруднено (например, в полевых условиях). При работе с источниками рентгеновского и гамма-излучений должна быть обеспечена биологическая защита.
Радиодефектоскопия основана на проникающих свойствах радиоволн сантиметрового и миллиметрового диапазонов (микрорадиоволн), позволяет обнаруживать дефекты главным образом на поверхности изделий обычно из неметаллических материалов. Радиодефектоскопия металлических изделий из-за малой проникающей способности микрорадиоволн ограничена (см. Скин-эффект). Этим методом определяют дефекты в стальных листах, прутках, проволоке в процессе их изготовления, а также измеряют их толщину или диаметр, толщину диэлектрических покрытий и т.д. От генератора, работающего в непрерывном или импульсном режиме, микрорадиоволны черезрупорные антенны проникают в изделие и, пройдя усилитель принятых сигналов, регистрируются приёмным устройством.
Инфракрасная Дефектоскопия использует инфракрасные (тепловые) лучи (см. Инфракрасное излучение) для обнаружения непрозрачных для видимого света включений. Так называемое инфракрасное изображение дефекта получают в проходящем, отражённом или собственном излучении исследуемого изделия. Этим методом контролируют изделия, нагревающиеся в процессе работы. Дефектные участки в изделии изменяют тепловой поток. Поток инфракрасного излучения пропускают через изделие и регистрируют его распределение теплочувствительным приёмником. Неоднородность строения материалов можно исследовать также методом ультрафиолетовой Дефектоскопии
Магнитная Дефектоскопия основана на исследовании искажений магнитного поля, возникающих в местах дефектов в изделиях из ферромагнитных материалов. Индикатором может служить магнитный порошок (закись-окись железа)или его суспензия в масле с дисперсностью частиц 5-10 мкм. При намагничивании изделия порошок оседает в местах расположения дефектов (метод магнитного порошка). Поле рассеяния можно фиксировать на магнитной ленте, которую накладывают на исследуемый участок намагниченного изделия (магнитографический метод). Используют также малогабаритные датчики (феррозонды), которые при движении по изделию в месте дефекта указывают на изменения импульса тока, регистрирующиеся на экране осциллоскопа (феррозондовый метод).
Электроиндуктивная (токовихревая) Дефектоскопия основана на возбуждении вихревых токов переменныммагнитным полем датчика дефектоскопа. Вихревые токи создают своё поле, противоположное по знаку возбуждающему. В результате взаимодействия этих полей изменяется полное сопротивление катушки датчика, что и отмечает индикатор. Показания индикатора зависят от электропроводности и магнитной проницаемости металла, размеров изделия, а также изменений электропроводности из-за структурных неоднородностей или нарушений сплошности металла.
Термоэлектрическая Дефектоскопия основана на измерении электродвижущей силы (термоэдс), возникающей в замкнутой цепи при нагреве места контакта двух разнородных материалов. Если один из этих материалов принять за эталон, то при заданной разности температур горячего и холодного контактов величина и знак термоэдс будут определяться химическим составом второго материала. Этот метод обычно применяют в тех случаях, когда требуется определить марку материала, из которого состоит полуфабрикат или элемент конструкции (в том числе и в готовой конструкции).
Электростатическая Дефектоскопия
основана на использовании электростатического поля, в которое помещают изделие. Для обнаружения поверхностных трещин в изделиях из неэлектропроводных материалов (фарфора, стекла, пластмасс), а также из металлов, покрытых теми же материалами, изделие опыляют тонким порошком мела из пульверизатора с эбонитовым наконечником (порошковый метод). При этом частицы мела получают положительный заряд. В результате неоднородности электростатического поля частицы мела скапливаются у краёв трещин. Этот метод применяют также для контроля изделий из изоляционных материалов. Перед опылением их необходимо смочить ионогенной жидкостью.
Рис. 5. Блок-схема ультразвукового эходефектоскопа: 1 - генератор электрических импульсов; 2 - пьезоэлектрический преобразователь (искательная головка); 3 - приёмно-усилительный тракт; 4 - хронизатор; 5 - генератор развёртки; 6 - электроннолучевая трубка; Н - начальный сигнал; Д - донный эхосигнал; ДФ - эхосигнал от дефекта.
Ультразвуковая Дефектоскопия
основана на использовании упругих колебаний (см. Упругие волны), главным образом ультразвукового диапазона частот. Нарушения сплошности или однородности среды влияют на распространение упругих волн в изделии или на режим колебаний изделия. Основные методы: эхометод, теневой, резонансный, велосимметрический (собственно ультразвуковые методы), импедансный и метод свободных колебаний (акустические методы).(рис. 5)
Резонансный метод основан на определении собственных резонансных частот упругих колебаний (частотой 1-10Мгц) при возбуждении их в изделии. Этим методом измеряют толщину стенок металлических и некоторых неметаллических изделий. При возможности измерения с одной стороны точность измерения около 1%. Кроме того, этим методом можно выявлять зоны коррозионного поражения. Резонансными дефектоскопами осуществляют контроль ручным способом и автоматизированным с записью показаний прибора.
Велосиметрический метод эходефектоскопии основан на измерении изменения скорости распространения упругих волн в зоне расположения дефектов в многослойных конструкциях, используется для обнаружения зон нарушения сцепления между слоями металла.
Импедансный метод основан на измерении механического сопротивления (импеданса) изделия датчиком, сканирующим поверхность и возбуждающим в изделии упругие колебания звуковой частоты. Этим методом можно выявлять дефекты в клеевых, паяных и др. соединениях, между тонкой обшивкой и элементами жёсткости или заполнителями в многослойных конструкциях. Обнаруживаемые дефекты площадью от 15 мм 2 и более отмечаются сигнализатором и могут записываться автоматически.
Метод свободных колебаний (см. Собственные колебания) основан на анализе спектра свободных колебаний контролируемого изделия, возбуждённого ударом; применяется для обнаружения зон нарушения соединений между элементами в многослойных клеёных конструкциях значительной толщины из металлических и неметаллических материалов.
Ультразвуковая Дефектоскопия , использующая несколько переменных параметров (частотный диапазон, типы волн, режимы излучения, способы осуществления контакта и др.), является одним из наиболее универсальных методов неразрушающего контроля.
Капиллярная Дефектоскопия основана на искусственном повышении свето- и цветоконтрастности дефектного участка относительно неповреждённого. Методы капиллярной Дефектоскопия позволяют обнаруживать невооружённым глазом тонкие поверхностные трещины и др. несплошности материала, образующиеся при изготовлении и эксплуатации деталей машин. Полости поверхностных трещин заполняют специальными индикаторными веществами (пенетрантами), проникающими в них под действием сил капиллярности. Для так называемого люминесцентного метода пенетранты составляют на основе люминофоров (керосин, нориол и др.). На очищенную от избытка пенетранта поверхность наносят тонкий порошок белого проявителя (окись магния, тальк и т.п.), обладающего сорбционными свойствами, за счёт чего частицы пенетранта извлекаются из полости трещины на поверхность, обрисовывают контуры трещины и ярко светятся в ультрафиолетовых лучах. При так называемом цветном методе контроля пенетранты составляют на основе керосина с добавлением бензола, скипидара и специальных красителей (например, красной краски). Для контроля изделий с тёмной поверхностью применяютмагнитный порошок, окрашенный люминофорами (магнитнолюминесцентный метод), что облегчает наблюдение тонких трещин.